Troy Bilt 3000 Psi Pressure Washer Manual 2 7 Gpm
Hi ted6565 Sounds like you have dirt/debris in your caburetor jets,fuel passages or a diaphgram that is becoming non-flexible. Check/Clean/Replace your Air Filter, a dirty air filter can make your engine run to rich with fuel. Note: ALWAYS USE COMPRESSED AIR TO CLEAN YOUR JETS AND PASSAGES, VERY IMPORTANT. Note:Before you disassemble the carburetor: Write down on a piece of paper and or take a picture of how the linkage attaches to your carburetor for later reference when you go to reinstall your carburetor. Mark each piece with a awl, or some kind of sharp instrument that will make an alignment scratch before you disassemble the carburetor into separate pieces. That way you will know which way it goes back together when you reassemble it. Sometimes you can get by with priming the carburetor or by using a very small shot of starting fluid and letting it run a few times like that, and it will flush the gunk out of the jets,but most of the time you will need to rebuild the carburetor.
Carburetor For Troy Bilt 0 PSI 2.7 GPM Pressure Washer B&S 875 8.75 See more like this. Troy-Bilt Pressure Washer 3000 psi Manual Model # 020242-1. Free Shipping. Carburetor Troy Bilt 3000 PSI 2.3 2.8 GPM Pressure Washer 7.0Hp Briggs &Stratton. I have a Troy Bilt pressure washer. 3000 psi/2.7 gpm, Briggs and Stratton engine. It starts fine as long as I hole the trigger on the wand. It will keep running and will work as needed.
Be sure to check your fuel tank for water and dirt/debris, if there is water/debris then you need to clean your tank. Check you fuel line/s condition.after a while they will degrade and need replacement. Check/Clean/Replace your fuel filter if you have one. When you remove your fuel lines from the carburetor be sure to make a drawing or take a picture of how the lines are connected to the carburetor.
Also a good time to take a picture for later reference for reassembly. If the mower is over a couple of years old, then I recommend that you buy and install a new carburetor repair kit,because the diaphragm will get hard and that will cause it to be hard to crank. The diaphgram may look good and flexible, but it can be deceiving and not act as a fuel pump as it should because it has become too hard and will cause hard starting,start and run and shut off, etc.
When you clean your carburetor, I recommend that you use a laquer thinner type cleaner to clean and dissolve the laquer build-up in the float and needle jet passages. Be sure to remove all plastic and rubber parts before using the laquer thinner because it can dissolve the plastic parts and render them unuseable. Be sure to use COMPRESSED AIR to blow out all the fuel and air passages.The higher air pressure is needed to blow some of the trash/debris from the fuel or air passages. Be careful when blowing out the passages, because there are sometimes small rubber type seats in the bottom of some of the passages. Keep in mind that the float (if you have one) for the carburetor must be level when you go to reassemble the carburetor or follow the instructions you get with the carburetor kit, or you could also ask the parts man that you get your kit from. When you clean your carburetor and remove the jet screws, you will first need to lightly seat the jet screws. But before you lightly seat the jet screws count the number of turns it takes to seat the jet screws from their original position.
Be sure to mark the turns down on a piece of paper. That way when you put the jets back in, you know to lightly seat them first and then turn them back out to their original position before you started. Once you have your carburetor cleaned/rebuilt that should solve your problem.
Please take time to rate me Bud Answered on Apr 23, 2013.
Published on March 18th, 2015 by Jacks 62 Troubleshooting Your Pressure Washer Warmer weather is on its way, so it’s time for some spring cleaning. You get your pressure washer out to do some outdoor washing, you try turning on the engine, and nothing happens. Or, you are in position to start washing, you pull the spray-gun trigger, and water doesn’t come out. First, step back and take a deep breath. Now let’s figure out how to troubleshoot your pressure washer.
Nozzle and Spray-gun Troubleshooting Your nozzle and spray gun are two important parts in your pressure washer to deliver the high pressure water spray. If these parts fail to work, here are some tips on getting them back in shape:. Inspect your nozzle, spray gun, connections and O-rings to make sure everything is tightened. Check if the nozzle, spray gun or inlet screen are clogged. Wash out if they are.

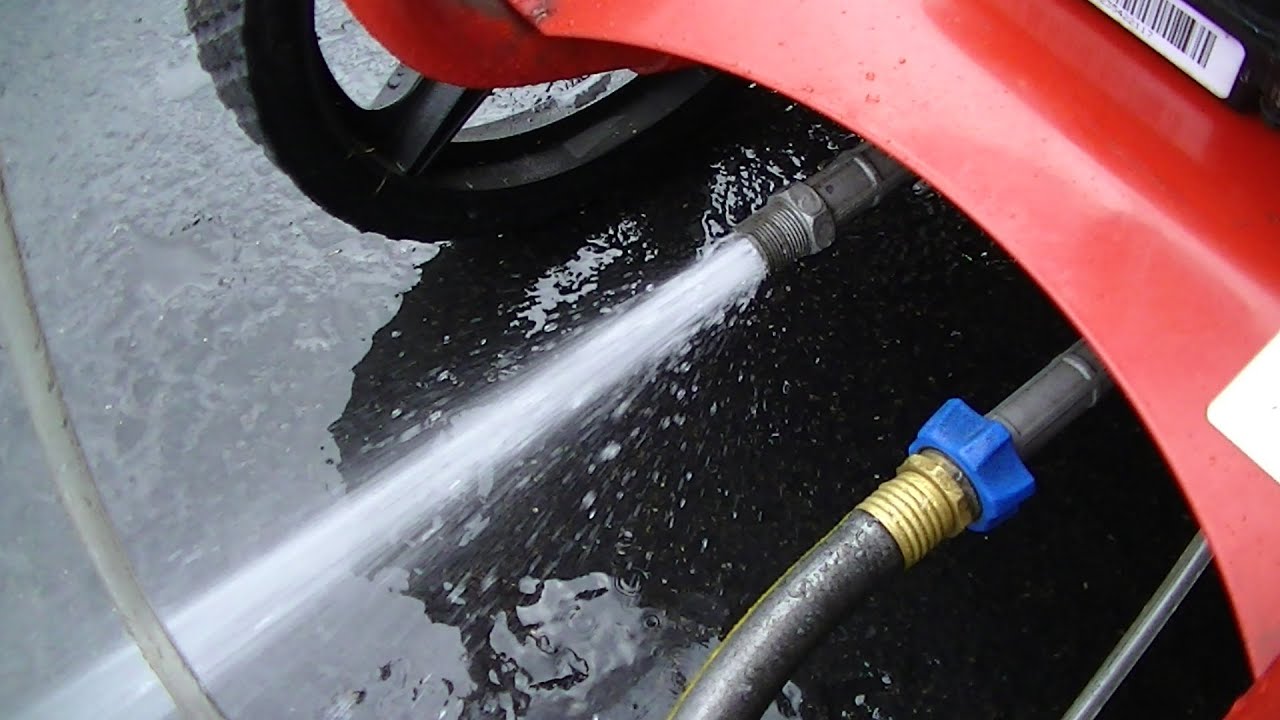
Replace O-rings if dirty or damaged. Inspect hose for any twist, cuts, bends or dents. Check your nozzle, hose, and spray gun for any clogs, dirt, and debris. Clean out or replace if needed. Your Engine Won’t Start or is Lacking Power If your gas-powered pressure washer engine does not start or is lacking power, there are a few things you can do. First, check the on/off switch to see if it is in the “on” position. However, before you touch anything, turn the engine off!
Even if it’s not running, turn the switch to the “off” position. You don’t want to inspect the engine while it is on, or could turn on, this could lead to serious injury and/or damage to the pressure washer engine. After you make sure the engine is off, here are some ways to check if it is running properly:. Run water through pressure washer until all air is removed from the hose. Check your air filter. Clean if dirty and replace if damaged. Check oil level.
Change if needed. Top off fuel in tank. If your fuel is more than 30 days old, dispose of it. Always use fresh gas. Make sure your spark plug is connected to the wire. If your engine was smoking:. Check if choke is on, return to off position.
Make sure there is an unrestricted air flow you’re your engine (clean your air filter). If You Find a Leak A leak in a pressure washer may have you at your wits end. However, some easy preventative maintenance can eliminate this. If for some reason it happens, here are some things to look over:. Inspect hose for any dents, cuts or twists, replace if damaged. Clean or replace O-rings, if that is where the leak is stemming from.
Tighten all of your connections. Make sure you are using the proper wand size for your pressure washer. Clean filter screens on the water intakes, replace if damaged or broken.
Troy Bilt 3000 Psi Pressure Washer Manual 2 7 Gpm Tankless Water
Low Pressure Won’t Help You Clean If the issue arises that your pressure washer isn’t providing you with the amount of pressure it should be, there are a few things that are easy to fix:. Make sure your nozzle is the right size and installed properly. Ensure that your nozzle is not in low PSI position.
Make sure your water supply is not restricted by anything (bends, cuts or damage to your garden hose). Look over your spray gun, nozzle and hose for any leaks. Check your nozzle, hose and spray gun for any clogs or dirt and debris. Clean out or replace if needed. Unloader Valve The unloader valve in the pressure washer is a very important part.
This keeps the pressure from building up when you aren’t spraying water. If your engine is dieing after you are finished spraying it, or you are experiencing low pressure without being able to identify the cause, it could be your unloader valve. If the unloader valve isn’t replaced when suspected to be damaged or broken, this could lead to low pressure, safety hazards, and damage to your pressure washer. In Conclusion: Pressure washers are a great cleaning tool, if you keep them working properly. The majority of your pressure washer malfunctions should be a simple fix.
Some preventative maintenance and occasional troubleshooting can keep your pressure washer in top shape and keep you cleaning without frustration. Jack’s Safety Tips: Before servicing or repairing any power equipment, disconnect the spark plug and battery cables.
Remember to wear appropriate safety glasses and gloves to protect against harmful chemicals and debris. Featured Parts and Products:. Tags. Having similar, Pressure washer will start, runs 3 mins cuts off. After 15 mins will start again runs 3 minutes with wand engaged and cuts off.
Also seems to not have the power it use to have, it is only 1 year old. I have replaced spark plug. I have empty gas tank and clean, I have rebuilt Carburetor (clean, replace needle value and set clean all port holes) everything look good.
Made no difference. I though at first it was a gas/ carburetor problem. Now I am just not sure. Did you ever get an answer to your question, My is a troybuilt pressure washer from lowes.Fresh out of warranty.
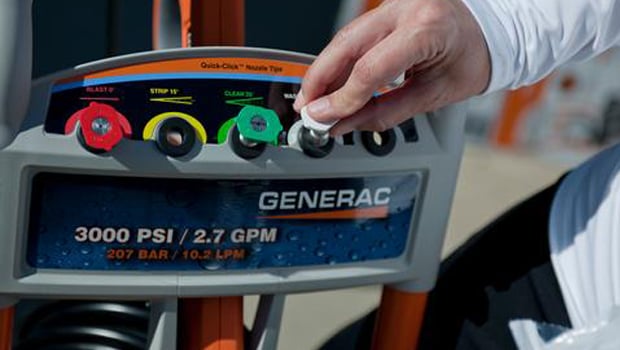
You can see a rubber boot or cover the size of a cigar butt, It’s at the pump. Remove the cover and pull out the clamp that goes through the casing that holds the uploader in.
With a flathead screw driver, pry the uploaded out by putting the screwdriver inside the spring nearest the casing and pry it out. There’s a stem at the back of the uploaded, make sure it moves freely, make sure o rings are in good shape, if not replace the unit, If alright put Vaseline on the o rings and and push the uploader back in and push the u shaped clamp back in. Check it out.
H1610 small electric power washer – I replaced the entire water path parts – the three sections were pre-assembled, so I believe they are correctly put together – inlet assembly, body assembly, manifold – and pump is working, but absolutely no water goes through pump passively when water source hooked up and turned on and pump motor still off. It used to leak through and bleed the air out before I started motor as instructed. And of course if turned on (briefly only to test) no water comes out then either. I can’t see any possible blockage and valves are all in correct direction – not a drop gets through, even with outlet hose off, so it’s not the trigger/nozzle. I’m experiencing the same issue at the moment. The pressure washer is basically brand-new and I’ve used it probably over a dozen times however I have you on the field cleaner in it after every use and always use fresh gas/change the oil Etc. The nozzle that intakes the fluid you are to be cleaning with can sometimes get clogged with sediment or other debris of you often use the unit to clean without the hose attached to it so I always keep mine intact since it has a filter attached to it, that just ensures that if the unit is in Proximity to debris/dirt while you are high pressure cleaning, none can be sucked into the intake the hose attaches to for solution-based cleaning.
I would suggest a large piece of heavy monofilament (fishing leader) or metal wire that you can stick into the intake to try and dislodge the debris your unit likely has sucked into the opening. Please let me know if anyone else has suggestions on this topic as it can be a frustrating endeavor, not unlike most issues with pressure washers. I have a Generac 2800 power washer that has new gas, oil, air filter, and checked oil levels and water pressure from city faucet. It is less that a year old and stored in a new shed. I make sure no pressure is in power hose and gun beyond a gentle spray thru. I start it with a half and or full choke that causes it to sputter to some life and immediately throttle up enough so it won’t run rough and I close the choke to off position. It runs smoothly with 1/3 throttle for about 2-3 minutes and will spray about a minute and die.
Restarted over and over again trying different minimal choke levels and throttle positions to no success. The results are it won’t start via throttle alone. It will start with choke and quickly add throttle while reducing choke and it will run smoothly at about 1/3 throttle afterward with no load or with load it dies. My arms, now as big as Popeye’s would thank you with appreciation if you would satisfy this mystery during our Hurricane cleanup. Have a 3000 psi Briggs and Stratton, have replaced carb, spark plug, fuel line and gas cap and using fresh fuel. Also checked on/off switch and wiring. When first starting the washer it starts after about 2 pulls and works fine for one tank of fuel.
After filling the fuel tank the washer will not start. Even after cooling. This occurs with the water line connected and turned on or off. If I leave the water running I have to trigger the wand and hold it while attempting to start the engineering. When attempting to start after running out of fuel, at times it has no compression, at other times it has too much compression. It may not start for several days then it starts great and runs great until it runs out of fuel.
I have reached a wall.